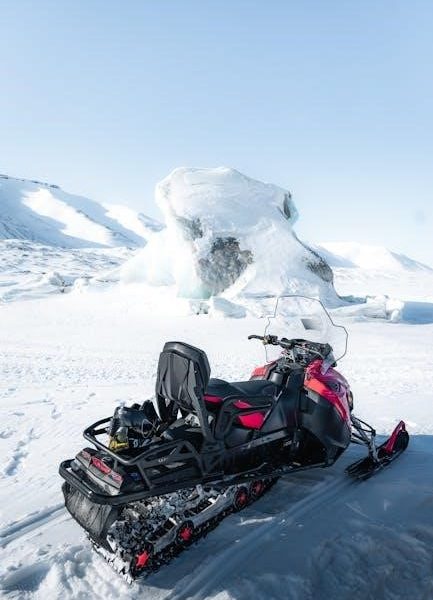
manitowoc ice machine troubleshooting guide
This guide provides essential insights into resolving common issues with Manitowoc ice machines, ensuring optimal performance and addressing key maintenance, error codes, and operational challenges effectively.
1.1 Importance of Regular Maintenance and Troubleshooting
Regular maintenance and troubleshooting are crucial for Manitowoc ice machines to ensure optimal performance and longevity. Proper care prevents issues like incomplete ice formation, low production, and unexpected shutdowns. Tasks such as descaling, cleaning condensers, and ensuring water pressure help maintain efficiency. Addressing problems early avoids costly repairs and downtime, ensuring consistent ice production and hygiene. Proactive maintenance also extends the machine’s lifespan and supports its overall functionality in commercial settings.
1.2 Common Issues Faced by Manitowoc Ice Machines
Manitowoc ice machines often encounter issues like incomplete ice formation, poor ice release, and operational shutdowns. Factors such as incorrect leveling, low water pressure, or dirty condensers can disrupt performance. Additionally, error codes related to temperature fluctuations or sensor malfunctions frequently occur. Regular maintenance, such as descaling and cleaning, is essential to prevent these problems and ensure smooth operation, addressing both mechanical and environmental challenges effectively.
Essential Pre-Troubleshooting Checks
Before addressing specific issues, verify the power supply, ensure proper water pressure, and check machine leveling to establish a baseline for effective troubleshooting procedures.
2.1 Checking Power Supply and Electrical Connections
Ensure the Manitowoc ice machine is receiving the correct voltage and power supply. Check all electrical connections for tightness and damage. Verify the circuit breaker hasn’t tripped and no fuses are blown. A stable power supply is crucial for operation. If issues persist, consult a licensed electrician to resolve any electrical problems before proceeding with further troubleshooting steps.
2.2 Ensuring Proper Water Supply and Pressure
A steady water supply and correct pressure are vital for Manitowoc ice machines. Check the water inlet valve for proper operation and ensure it’s fully open. Verify that water pressure meets the manufacturer’s specifications, typically between 20-80 PSI. Low pressure or restricted flow can disrupt ice production. Inspect for blockages in water lines or filters and clean or replace them as needed to maintain consistent water flow and machine performance.
2.3 Verifying Machine Leveling
Proper leveling is crucial for Manitowoc ice machines to function efficiently. Use a spirit level to ensure the machine is perfectly horizontal. Check both front-to-back and side-to-side alignment. Adjust the machine’s legs as needed to achieve balance. Improper leveling can cause uneven ice production or operational issues. Ensure the surface is firm and even to support the machine’s weight and maintain optimal performance throughout its operation cycle.
Common Operational Issues and Solutions
Addressing issues like ice not releasing, hollow cubes, or the machine not turning on is crucial. Solutions often involve cleaning, leveling, or adjusting internal components for optimal performance.
3.1 Ice Machine Not Turning On
If your Manitowoc ice machine won’t turn on, check the power supply, circuit breakers, and fuses. Ensure the machine is properly plugged in and the outlet is functioning. Verify the water supply is on and the control board is clean. Check for tripped switches or blown fuses. Also, inspect the on/off switch and ensure the machine is correctly installed. Addressing these issues can often resolve the problem quickly and restore operation.
3.2 Ice Not Releasing Properly
If the ice is not releasing properly, check if the machine is dirty or scaling, which can block ice release. Ensure the machine is level, as improper leveling can disrupt ice ejection. Low air temperature around the unit may also cause issues. Additionally, inspect the ice thickness probe for proper adjustment. Clean or descale the machine if necessary, and ensure the harvest float switch is functioning correctly to resolve the issue effectively.
3.3 Producing Hollow, Shallow, or Incomplete Ice Cubes
Hollow, shallow, or incomplete ice cubes often result from improper water level settings or an incorrectly adjusted ice thickness probe. Ensure the water supply is stable and within the recommended pressure range. Check for scaling or dirt buildup, which can disrupt water flow. Clean and descale the machine if necessary. Adjust the ice thickness probe to ensure it accurately measures ice formation. Proper alignment and cleanliness of components will resolve this issue effectively.
Understanding Manitowoc Ice Machine Error Codes
Manitowoc error codes identify specific issues, from mechanical faults to environmental factors. Understanding these codes is crucial for quick diagnosis and effective troubleshooting to maintain optimal performance.
4.1 List of Common Error Codes and Their Meanings
Manitowoc ice machines display specific error codes to indicate issues. Common codes include those for extended freeze cycles, low water flow, and high condenser temperatures. Each code corresponds to a specific problem, such as faulty sensors, blocked water filters, or poor ventilation. Understanding these codes helps pinpoint the root cause, enabling targeted repairs and minimizing downtime. Refer to the Indigo Series event log for a detailed list of codes and their explanations.
4.2 How to Use the Indigo Series Event Log
The Indigo Series event log is a valuable tool for diagnosing issues with Manitowoc ice machines. Access the log via the machine’s control panel to view recorded error codes, operational data, and maintenance alerts. By reviewing these records, users can identify recurring problems, track machine performance, and perform timely repairs. This feature helps in proactive maintenance, reducing unexpected breakdowns and ensuring continuous ice production. Regularly checking the event log is essential for optimal machine functionality.
Advanced Troubleshooting Steps
Advanced troubleshooting involves cleaning the condenser, descaling, and checking the ice thickness probe and harvest float switch to ensure optimal performance and resolve complex issues effectively.
5.1 Cleaning the Condenser and Air Filters
Cleaning the condenser and air filters is crucial for maintaining efficient operation. A dirty condenser can cause high energy consumption and poor performance. Turn off the machine, then use a soft brush or vacuum to remove dust and debris from the condenser coils. Also, inspect and clean air filters regularly to ensure proper airflow. This step helps prevent overheating and extends the machine’s lifespan. Clean every 1-3 months, depending on usage and environment conditions.
5.2 Descale and Sanitize the Machine
Descaling and sanitizing are crucial for maintaining Manitowoc ice machines. Mineral buildup from hard water can reduce efficiency and ice quality. Regular descaling removes these deposits, ensuring optimal performance. Sanitizing prevents mold and bacterial growth, keeping the machine hygienic. Perform these tasks every 3 to 6 months, depending on water hardness and usage levels. Always follow the manufacturer’s guidelines for best results and to extend the machine’s lifespan.
5.3 Checking the Ice Thickness Probe and Harvest Float Switch
Regularly inspecting the ice thickness probe and harvest float switch ensures proper ice production. The probe monitors ice thickness, while the float switch controls the harvest cycle. If misaligned or dirty, they can cause incomplete or oversized ice cubes. Clean or adjust these components as needed to maintain consistent ice formation and prevent operational disruptions. Proper calibration ensures efficient and reliable ice machine performance, avoiding common issues like overfilling or underfilling ice molds. Regular checks prevent unexpected breakdowns and extend machine lifespan.
Preventative Maintenance Tips
Regular cleaning, descaling, and water supply checks are crucial. Monitor air temperature and humidity. Schedule professional servicing to ensure optimal performance and longevity of your Manitowoc ice machine.
6.1 Schedule Deep Cleaning and Maintenance
Regular deep cleaning and maintenance are vital to ensure Manitowoc ice machines operate efficiently. Descale the machine every 3-6 months, especially in hard water areas, to prevent scaling. Clean the condenser and air filters monthly to maintain proper airflow. Sanitize all components to prevent bacterial growth. Schedule professional servicing annually to inspect and replace worn parts, ensuring long-term reliability and optimal ice production.
6.2 Monitoring Air Temperature Around the Machine
Monitoring air temperature around the Manitowoc ice machine is crucial for optimal performance. Ensure the machine is placed in an area with adequate ventilation and ambient temperatures between 40°F and 90°F. Excessive heat can reduce efficiency and cause the machine to overwork, while low temperatures may affect ice production. Regularly check the surrounding air temperature and ensure proper clearance from nearby equipment to maintain consistent operation and longevity.
6.3 Proper Installation and Care Guidelines
Proper installation and care are vital for the longevity and efficiency of your Manitowoc ice machine. Ensure the machine is installed on a level surface, away from direct sunlight, and in a well-ventilated area. Regularly clean the exterior and internal components to prevent dust buildup. Follow the manufacturer’s guidelines for water supply, electrical connections, and drainage. Proper installation and routine maintenance ensure consistent ice production, reduce wear and tear, and prevent unexpected breakdowns.
Diagnostic Tools and Resources
Essential tools include multimeters, pressure gauges, and flashlights for inspecting internal components. Utilize Manitowoc’s troubleshooting guides and manuals for comprehensive diagnostics and detailed repair instructions.
7.1 Using a Flashlight to Inspect Internal Components
A flashlight is a crucial tool for visually inspecting internal parts of your Manitowoc ice machine. Start by ensuring the machine is turned off and safe to access. Shine the light to examine the condenser, evaporator, and ice-making components for dirt, blockages, or damage. This step helps identify issues like dirty coils or misaligned parts before they escalate. Regular inspections can prevent costly repairs and downtime.
7.2 Manitowoc Troubleshooting Guides and Manuals
Manitowoc provides comprehensive troubleshooting guides and manuals to help diagnose and resolve issues efficiently. These resources include detailed diagrams, error code explanations, and step-by-step repair instructions. They cover common problems like dirty condensers, incorrect water levels, and faulty sensors. By following these guides, users can address issues independently, ensuring minimal downtime and optimal performance. Always refer to the official Manitowoc documentation for accurate and model-specific troubleshooting advice.
8.1 Summary of Key Troubleshooting Steps
Key steps include checking power supply, water pressure, and machine leveling. Clean condensers, descale, and sanitize regularly. Monitor air temperature and inspect internal components with a flashlight. Address error codes promptly and refer to the event log for detailed insights. Ensure proper installation and maintenance to prevent issues. If problems persist, consult Manitowoc’s troubleshooting guides or contact a professional technician for assistance.
8.2 When to Call a Professional Technician
Contact a technician if issues persist after basic troubleshooting steps. Seek professional help for complex repairs, such as internal component malfunctions or recurring error codes. If safety is at risk or repairs require specialized tools, do not attempt DIY fixes. Persistent problems like repeated breakdowns or severe ice production issues also warrant expert intervention to ensure proper resolution and prevent further damage.
Related posts:
Archives
Calendar
M | T | W | T | F | S | S |
---|---|---|---|---|---|---|
1 | 2 | 3 | 4 | 5 | 6 | |
7 | 8 | 9 | 10 | 11 | 12 | 13 |
14 | 15 | 16 | 17 | 18 | 19 | 20 |
21 | 22 | 23 | 24 | 25 | 26 | 27 |
28 | 29 | 30 | 31 |
Leave a Reply
You must be logged in to post a comment.